Understanding the Maturity Method in Concrete Construction
Developer
October 4, 2024
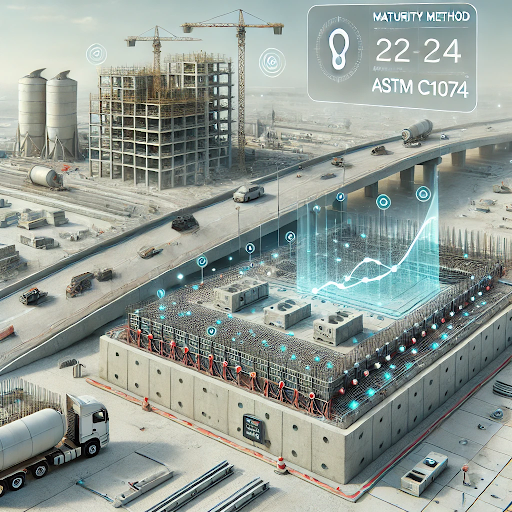
Introduction
The Maturity Method is a non-destructive technique commonly used in the concrete industry to estimate the real-time strength of in-place concrete. Standardized under ASTM C1074, this method is essential in modern construction, allowing for more accurate and timely decisions at key stages. It aids in tasks such as formwork removal, post-tensioning, opening roadways to traffic, ensuring compliance with DOT thermal control plans, and helping precasters determine the optimal and safest time to remove concrete elements from molds.
What is the Maturity Method?
The Maturity Method is based on the principle that concrete strength is directly related to its temperature history. Essentially, concrete of the same mix design that reaches the same maturity index will achieve the same strength, regardless of the curing conditions. The maturity index is calculated either by the temperature-time factor or the equivalent age, which takes into account the concrete’s temperature history and how long it has been curing.
Why is the Maturity Method Important?
Traditionally, concrete strength is determined through break tests of cured cylinders. However, these tests require waiting for several days to obtain results, causing delays in the construction process. The Maturity Method eliminates this waiting period, providing real-time strength estimates that allow construction to proceed more efficiently and safely.
By implementing the Maturity Method, contractors can reduce construction downtime by approximately 20%, cut down project schedules by about two days per pour, and save up to $10,000 per day on projects. This method not only accelerates project timelines but also enhances overall project efficiency.
How Does the Maturity Method Work?
The process begins with developing a strength-maturity relationship for a specific concrete mix in the laboratory. This involves preparing test specimens, monitoring their temperature history, and conducting compression tests at various ages (typically 1, 3, 7, 14, and 28 days). The results are then plotted to create a maturity curve that can be used on-site to estimate the in-place strength of the concrete.
During construction, sensors are embedded in the concrete to monitor temperature over time. The maturity index is continuously calculated, allowing the construction team to estimate when the concrete has reached the desired strength for further construction activities.
Applications and Benefits of the Maturity Method
- Formwork Removal: Knowing the precise strength of the concrete in real-time allows for the safe and timely removal of formwork, reducing the risk of structural damage.
- Post-Tensioning: Accurate strength measurements ensure that post-tensioning is done at the optimal time, avoiding potential issues like cracking.
- Saw Cutting and Opening Roads: Contractors can determine the ideal time to saw cut joints or open roads to traffic without compromising the structural integrity of the concrete.
- Mix-Design Optimization: By analyzing maturity data, engineers can optimize the mix design, potentially reducing the amount of cement required without sacrificing strength.
SensyRoc™ and the Maturity Method
SensyRoc™, a wireless concrete sensor, revolutionizes the implementation of the Maturity Method by providing real-time monitoring of concrete strength and other critical parameters like temperature and electrical resistivity. This sensor simplifies the maturity monitoring process, offering a user-friendly interface through an Android and iOS app that displays live data and generates comprehensive reports.
By integrating SensyRoc™ into your concrete projects, you can further enhance efficiency, reduce reliance on traditional cylinder tests, and ensure higher quality and safety in your construction practices.
Conclusion
The Maturity Method represents a significant advancement in concrete technology, allowing for more precise, real-time monitoring of concrete strength. By adopting this method, construction projects can achieve faster timelines, lower costs, and better overall outcomes. SensyRoc™ sensors bring this method into the digital age, offering a robust tool for any project looking to improve its concrete quality control processes.